The Influence of Welding Inspection Milwaukee on Job Success and Conformity
The Influence of Welding Inspection Milwaukee on Job Success and Conformity
Blog Article

Discovering the Various Approaches and Specifications of Welding Inspection for Achieving Compliance and Dependability in Engineering Applications
The importance of welding evaluation in design applications can not be overemphasized, as it acts as a critical guard for ensuring structural stability and compliance with industry requirements. Various methods, including aesthetic inspection and advanced non-destructive screening strategies, give vital insights right into the top quality of welds. In addition, adherence to recognized regulative standards such as those from AWS and ASME establishes a structure for accountability and quality. However, the landscape of welding examination is constantly evolving, prompting a closer evaluation of arising techniques and their implications for design dependability. What might these advancements involve for future tasks?
Relevance of Welding Inspection
Welding assessment plays a vital role in guaranteeing the stability and safety of welded structures. This procedure entails the methodical examination of welds to confirm compliance with predetermined requirements and requirements. The significance of welding evaluation can not be overstated, as it works as a secure versus possible failings that could result from inadequate welding techniques. With extensive examination, defects such as fractures, voids, and inadequate fusion can be determined early, thereby stopping catastrophic failures that might bring about structural collapse or safety and security threats.
Additionally, welding examination is necessary for preserving quality control throughout the welding procedure. It ensures that the welds fulfill the essential mechanical and physical properties needed for their intended applications. Regular examinations also foster a culture of liability and continuous improvement within welding operations, encouraging adherence to ideal practices and market criteria.
In regulated sectors such as building, aerospace, and manufacturing, rigorous welding assessment procedures are mandated to comply with legal and safety requirements. Ultimately, reliable welding evaluation not only shields human life and residential property yet likewise enhances the long life and integrity of bonded structures, making it an indispensable aspect of engineering and building and construction.
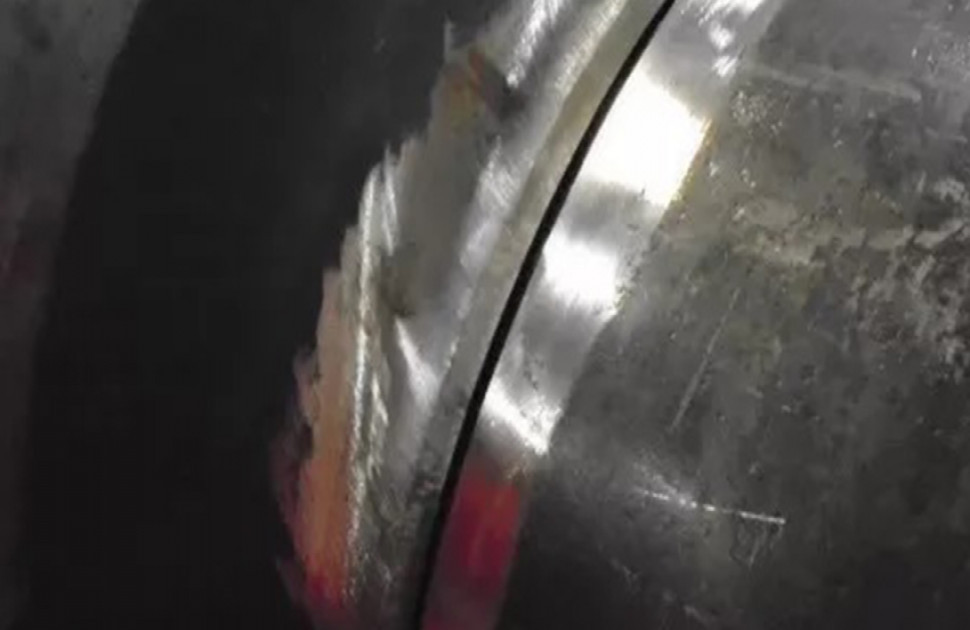
Usual Welding Evaluation Techniques
A selection of examination approaches are utilized to analyze the quality and honesty of welds, each customized to find certain kinds of defects. Amongst the most common techniques is visual evaluation, which involves a thorough evaluation of the weld surface to identify noticeable problems such as cracks, undercuts, and poor combination. This technique is typically the initial step in the evaluation process because of its simplicity and cost-effectiveness.
Another widely utilized approach is radiographic examination, where X-rays or gamma rays permeate the weld to expose inner defects. This method is specifically effective for finding porosity and incorporations within the weld product. Similarly, ultrasonic screening employs high-frequency sound waves to determine inner problems, providing a thorough evaluation of the weld's integrity.
Additionally, magnetic bit assessment is utilized for ferromagnetic materials, enabling the discovery of surface and near-surface issues by applying electromagnetic fields and observing particle patterns. Dye penetrant testing involves applying a fluid dye to the weld surface area, disclosing cracks and other gaps upon examination (Welding Inspection Milwaukee). Each of these techniques plays a crucial function in making certain weld top quality and conformity with industry criteria
Non-Destructive Checking Strategies
Non-destructive testing (NDT) methods are vital devices in the analysis of weld quality, permitting inspectors to examine the stability of bonded joints without creating damages to the products. Various NDT techniques are employed to recognize prospective issues, guaranteeing that welds satisfy the called for criteria for safety and security and efficiency.
One of one of the most common methods is ultrasonic testing (UT), which utilizes high-frequency sound waves to spot interior defects such as cracks or voids. Radiographic testing (RT) uses X-rays or gamma rays to create pictures of welds, disclosing any interruptions within the material. Magnetic bit testing (MT) works for finding surface area browse around here and near-surface issues in ferromagnetic products with the application of electromagnetic fields and contrasting particles.
Liquid penetrant testing (PT) is an additional commonly made use of approach that involves applying a dye to the surface area of the weld, which leaks right into any cracks, making them visible under ultraviolet light. Each of these methods offers unique benefits and limitations, and the choice of a proper method is critical to accomplishing accurate evaluations of weld stability. Eventually, the execution of NDT methods significantly contributes to the dependability and security of design applications.
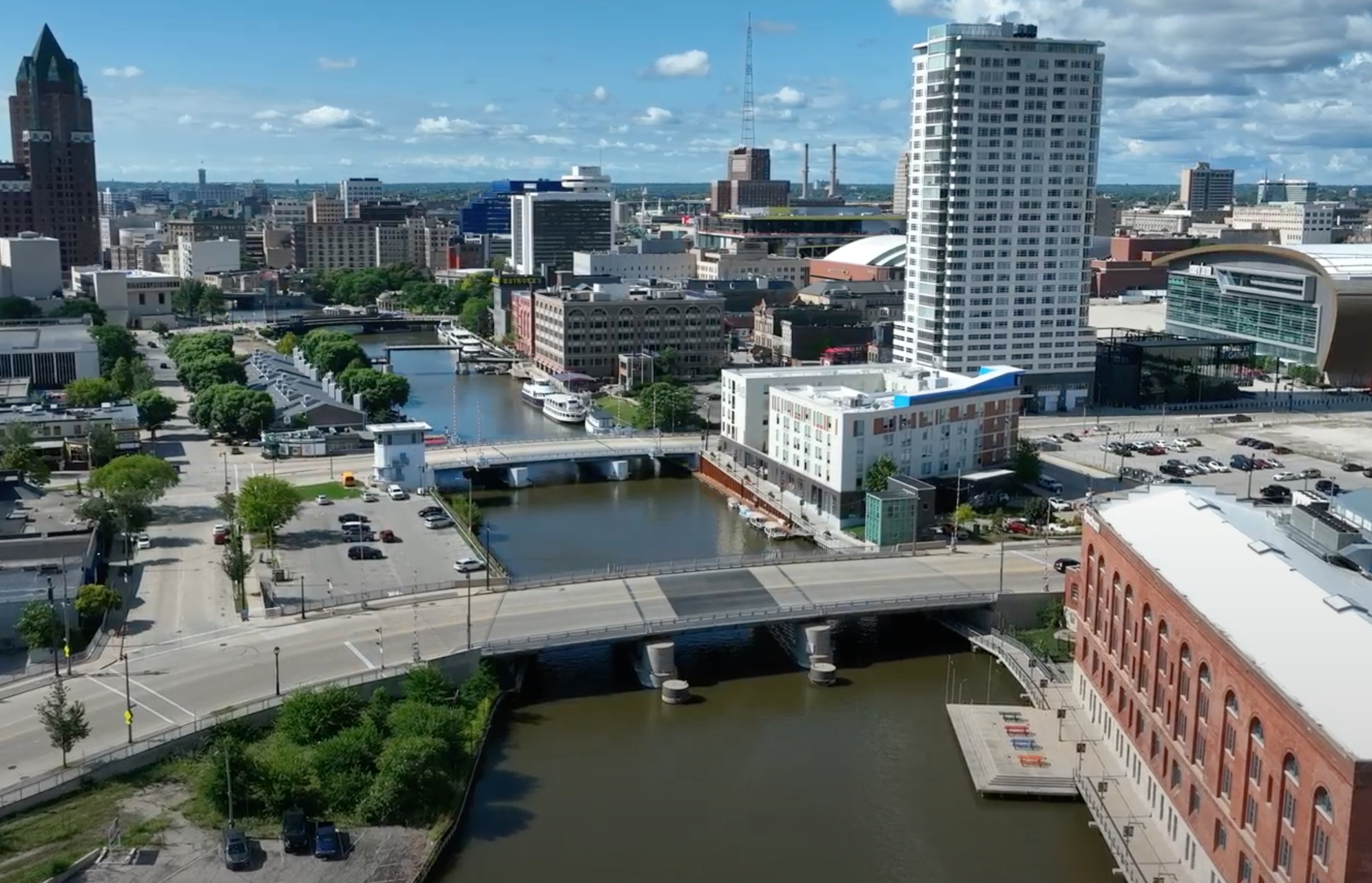
Regulatory Standards and Conformity
In the realm of welding assessment, adherence to regulatory criteria and conformity is paramount to make certain the security and dependability of bonded structures (Welding Inspection Milwaukee). Various companies, consisting of the American Welding Culture (AWS), the American Society of Mechanical Engineers (ASME), and the International Company for Standardization (ISO), have established standards that regulate welding methods and assessment treatments. These standards offer a framework for quality control, detailing the required qualifications for inspectors and the methods for examining weld honesty
Compliance with these governing requirements not only enhances the structural integrity of welded settings up but also minimizes threats related to failures, which can have disastrous effects. Evaluations need to be carried out utilizing defined procedures, including visual, ultrasonic, and radiographic methods, to make certain that welds satisfy specified criteria.
Additionally, adherence to these requirements is often needed by law, particularly in sectors such as aerospace, manufacturing, and construction. Regular audits and certifications are necessary to preserve compliance, therefore cultivating a culture of safety and high quality within organizations. Eventually, regulative criteria and compliance act as the foundation of reliable welding inspection techniques, making sure that crafted frameworks meet both efficiency expectations and safety requirements.
Best Practices for Welding Assessment
While maintaining compliance with regulatory criteria is essential, executing ideal methods for welding examination further enhances the security and stability of welded frameworks. Reliable welding inspection begins with extensive planning, that includes comprehending the specific needs of each job and making certain examiners are trained in suitable approaches and standards.
Utilizing a thorough examination list assists to make sure all crucial elements are evaluated, such as weld dimension, infiltration, and aesthetic issues. Non-destructive testing (NDT) strategies, such as radiographic or ultrasonic testing, should be utilized where suitable, offering a more thorough evaluation of weld top quality without endangering the stability of the materials.
Documents plays a considerable duty in best methods; preserving exact records of inspections, consisting of pictures, examination results, and compliance records, makes certain liability and facilitates future assessments. Additionally, promoting a culture of open communication between welders and assessors can bring about early Visit This Link identification of possible problems, advertising immediate restorative activities.
Conclusion
In summary, the implementation of rigorous welding assessment methods and adherence to established requirements are essential for making certain compliance and reliability in engineering applications - Welding Inspection Milwaukee. Methods such as visual evaluation, radiographic testing, and ultrasonic testing act as vital devices in maintaining and identifying defects high quality guarantee. By fostering a society of responsibility and excellence, companies can improve the integrity and durability of bonded structures, eventually adding to the safety and efficacy of design tasks
Different techniques, consisting of visual evaluation and advanced non-destructive screening techniques, give vital insights into the top quality of welds.Welding evaluation plays an essential function in making sure the honesty and safety and security of welded frameworks.A variety of assessment methods are used to analyze the quality and stability of welds, each tailored to discover specific kinds of flaws.An additional extensively used method is radiographic evaluation, sites where X-rays or gamma rays permeate the weld to disclose interior defects.In the world of welding inspection, adherence to regulative criteria and conformity is vital to guarantee the safety and security and integrity of welded structures.
Report this page